Three Sources of Catalyst Deactivation and How To Mitigate Them
ChemCatBio 2023 Technology Brief
This ChemCatBio Technology Brief reviews current knowledge on catalyst deactivation and mitigation for thermo-catalytic processes in biomass conversion, detailing three primary causes of catalyst deactivation and key strategies for mitigating them.
To reach commercial viability, biomass conversion industries need catalysts to be stable enough to operate for months or even years. But catalyst deactivation—a chemical or mechanical issue that limits or prevents desired chemical reactions—can greatly reduce the lifetime of catalysts and the durability of the process. This ChemCatBio Technology Brief highlights three common sources of catalyst deactivation: (1) structural damage by water, (2) poisoning by contaminants, and (3) fouling by coke. It also outlines key strategies for mitigating catalyst deactivation, equipping researchers with information and resources for designing more stable, resilient, and economical catalytic conversion processes.
What Mechanisms Drive Catalyst Deactivation?
Three Sources of Catalyst Deactivation From Biomass-Derived Feedstocks
Case Study: Potassium Deactivation of Pt/TiO2 Catalysts
Four Ways To Mitigate Catalyst Deactivation
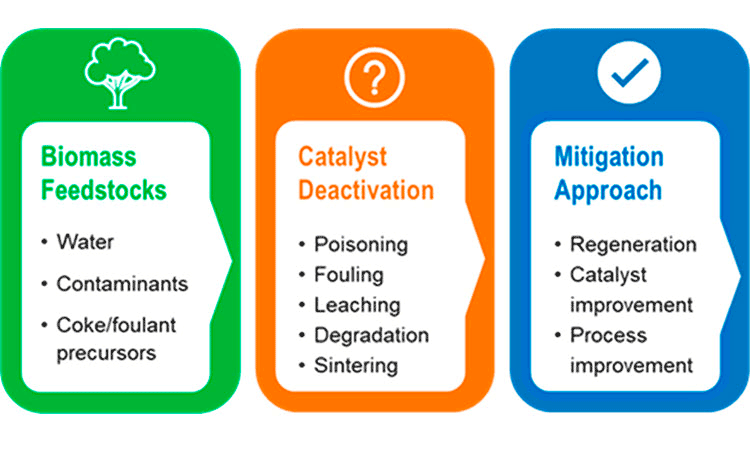
Catalyst Deactivation and Its Mitigation During Catalytic Conversions of Biomass
ACS Catalysis, 2022
Huamin Wang
[email protected]
509-371-6705
Case Study: Potassium Deactivation of Pt/TiO2 Catalysts
The Challenge: Potassium Accumulates on Pt/TiO2, a Catalyst Used in Catalytic Fast Pyrolysis
During catalytic fast pyrolysis, potassium—an abundant metallic contaminant in woody biomass—can deposit on the surface of the catalyst, platinum on titanium dioxide (Pt/TiO2), at the atomic level. The effect on the catalyst active sites and therefore catalyst stability was unclear.
The Approach: Combine Detailed Characterization and Catalytic Activity Measurements To Probe the Influence of Potassium
Researchers simulated potassium accumulation on Pt/TiO2. They then characterized the properties of the catalyst with various techniques, gathering kinetic measurements of several reactions to establish the correlation of potassium distribution with the change of catalytic sites.
The Findings
- Poisoning Occurs at Lewis Acid Sites: The Pt/TiO2 catalyst was deactivated by potassium via the poisoning of Lewis acid Ti sites, both on the TiO2 support and at the metal−support interface. The metallic Pt clusters remained largely uncontaminated.
- Potassium Poisoning Is Reversible: Water washing can successfully remove the accumulated potassium and recover the catalyst’s activity.
Four Ways To Mitigate Catalyst Deactivation
- Deal with it early: Consider deactivation during early catalyst research and development. Fully assess the actual biomass-derived feedstock to identify properties that may cause catalyst failure at industrially relevant conditions.
- Understand it better: Conduct research for a deeper understanding of catalyst deactivation mechanisms during biomass conversion. In situ and operando characterization methods can probe changes in catalyst active sites and the formation of surface species during reactions. Also, perform extended-duration experiments to evaluate catalysts after their initial “break-in” period.
- Measure it correctly and quickly: Study catalyst deactivation under kinetically-controlled conditions. Try to quantify deactivation, such as measuring the loss rate of active sites. To save time and money, develop accelerated catalyst aging processes to simulate catalyst deactivation. Multiscale, sophisticated, and realistic computational models can help demystify catalyst deactivation and, more importantly, predict catalyst stability for long-term operation.
- Look beyond the catalyst: Take a holistic approach to address catalyst deactivation by both improving catalysts and process design. Techno-economic analysis can provide powerful insights into economic feasibility and key impact factors related to catalyst stability with more rational and rigorous assumptions on catalyst lifetime.